Table of Contents
1. Introduction
Automation plays a crucial role in modern industrial engineering, revolutionizing manufacturing processes and increasing efficiency. This article will explore the key principles of automation in industrial engineering, highlighting the benefits and challenges associated with its implementation.
2. Definition of Automation
Automation refers to the use of various technologies and systems to control and operate machinery and processes with minimal human intervention. It involves the integration of hardware, software, and communication systems to streamline and optimize industrial operations.
3. Importance of Automation in Industrial Engineering
Automation brings several significant advantages to industrial engineering, contributing to improved efficiency, cost reduction, quality enhancement, and safety.
4. Efficiency and Productivity
Automation eliminates repetitive and mundane tasks, allowing workers to focus on more complex and value-added activities. By optimizing workflows and minimizing downtime, automation significantly improves productivity in industrial settings.
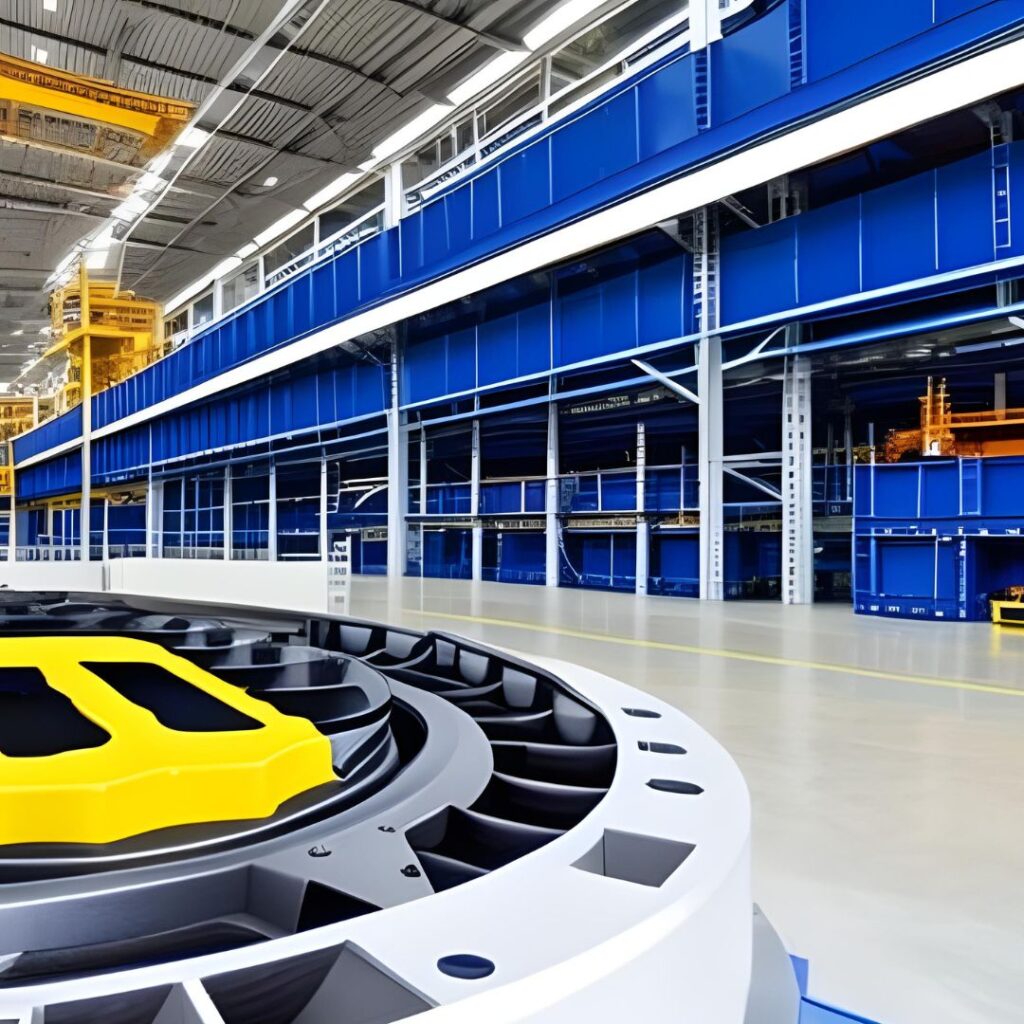
5. Cost Reduction
By automating processes, businesses can achieve cost savings in various areas. Automation reduces labor costs, decreases material waste, optimizes energy usage, and enhances resource allocation. These cost reductions ultimately lead to improved profitability.
6. Quality Improvement
Automation ensures consistent and precise manufacturing processes, reducing human errors and variability. By eliminating manual intervention, it enhances product quality, resulting in higher customer satisfaction and reduced rework or rejection rates.
7. Safety Enhancement
Industrial automation reduces workers’ exposure to hazardous environments and high-risk tasks. By automating dangerous or physically demanding processes, it minimizes the risk of accidents, injuries, and work-related illnesses, creating a safer work environment.
8. Key Principles of Automation
To successfully implement automation in industrial engineering, certain key principles need to be considered.
9. Principle 1: Standardization
Standardization involves developing and following uniform processes and specifications across different stages of production. By standardizing equipment, components, and procedures, automation becomes more seamless and efficient.
10. Principle 2: Integration
Integration refers to the seamless connection and coordination between various automated systems, equipment, and software. It involves integrating sensors, control systems, data networks, and communication protocols to ensure smooth operation and data flow.
11. Principle 3: Scalability
Scalability is the ability of an automation system to accommodate changing production demands and volumes. A scalable automation setup allows businesses to expand or modify their operations without significant disruptions or costly investments.
12. Principle 4: Flexibility
Flexibility in automation enables quick adaptation to changes in product specifications or market demands. It involves designing systems and processes that can be easily reconfigured or reprogrammed to accommodate variations in production requirements.
13. Principle 5: Continuous Improvement
Continuous improvement is a fundamental principle in automation. It involves regularly evaluating and optimizing automated processes, identifying areas for enhancement, and implementing iterative improvements to achieve higher efficiency and effectiveness.
14. Challenges in Implementing Automation
Implementing automation in industrial engineering can pose certain challenges that need to be addressed for successful deployment.
One major challenge is the initial investment required for acquiring automation equipment and systems. The cost of implementing automation can be significant, especially for small and medium-sized enterprises. However, it’s important to consider the long-term benefits and return on investment that automation brings, including improved productivity and cost savings.
Another challenge is the need for skilled personnel to operate and maintain automated systems. As automation technology advances, there is a growing demand for workers with specialized knowledge in robotics, control systems, and data analysis. Ensuring a competent workforce with the necessary skills is crucial for maximizing the benefits of automation.
Integration of automation systems with existing infrastructure can also be a challenge. Compatibility issues, data integration, and connectivity problems may arise when integrating new automation technology with legacy systems. Adequate planning and collaboration between different departments and stakeholders are essential to overcome these integration challenges.
Moreover, resistance to change and fear of job displacement among employees can hinder the adoption of automation. It’s important to address these concerns through effective communication and providing training opportunities to help employees adapt to new roles and responsibilities in the automated environment.
Lastly, cybersecurity is a critical concern when implementing automation. With increased connectivity and reliance on digital systems, industrial processes become vulnerable to cyber threats. Robust cybersecurity measures, including network security protocols, data encryption, and employee awareness training, must be in place to protect against potential breaches and ensure the integrity and safety of automated systems.
In conclusion, automation brings significant benefits to industrial engineering, including improved efficiency, cost reduction, quality enhancement, and safety. By adhering to key principles such as standardization, integration, scalability, flexibility, and continuous improvement, businesses can maximize the advantages of automation. However, it is important to address challenges related to initial investment, skilled workforce, integration, employee resistance, and cybersecurity to ensure successful implementation. Embracing automation while proactively managing these challenges will help industrial engineering enterprises stay competitive in today’s rapidly evolving market.
Reference: Youtube Video By Professor Murray
About ELGC
We have recently attained the ISO9001-2015 certification for Constructional and Engineering Contracting related to Technology Projects in addition to the other activities.
FAQs
Will automation eliminate jobs in industrial engineering?
While automation may replace certain repetitive tasks, it also creates new job opportunities. Skilled workers are needed to operate, maintain, and program automated systems. Automation allows employees to focus on higher-value activities, driving innovation and growth.
Can automation be implemented in all types of industries?
Yes, automation can be implemented in various industries, including manufacturing, logistics, healthcare, and more. The level and extent of automation may vary depending on the specific needs and processes of each industry.
How long does it take to implement automation in industrial engineering?
The implementation timeline for automation can vary depending on factors such as the complexity of processes, scale of operations, and available resources. It is crucial to plan and execute the implementation process systematically to ensure a smooth transition.
What are the potential risks associated with automation?
Some potential risks include technical failures, cybersecurity threats, and job displacement concerns. However, these risks can be mitigated through proper planning, risk assessment, and proactive measures to address potential challenges.
Can automation improve sustainability in industrial engineering?
Yes, automation can contribute to sustainability by optimizing resource usage, reducing waste, and minimizing environmental impact. Automated systems can be designed to operate more efficiently and consume fewer resources, promoting sustainable practices.